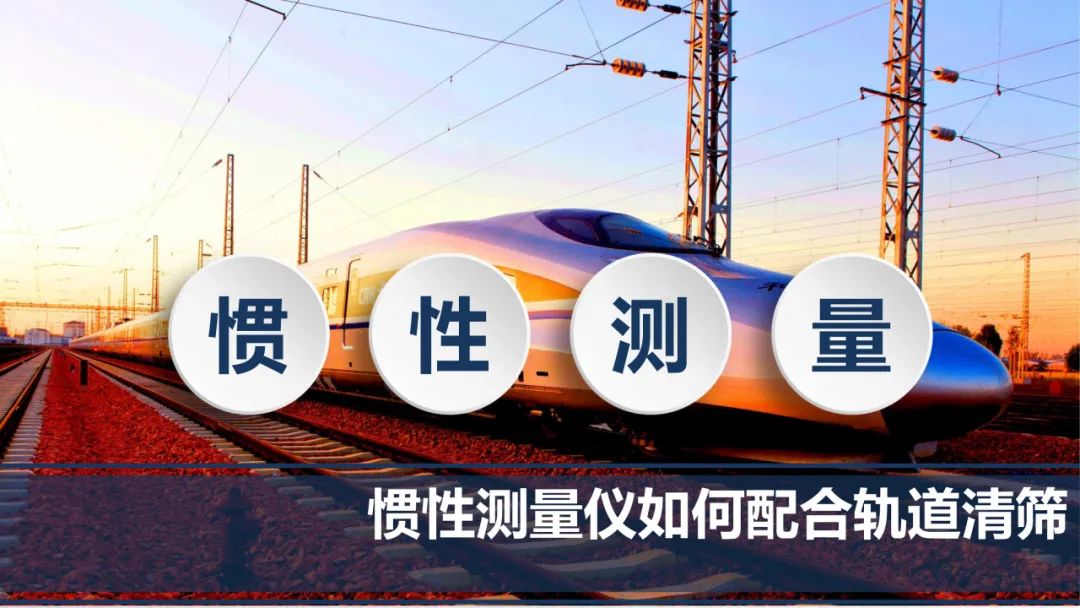
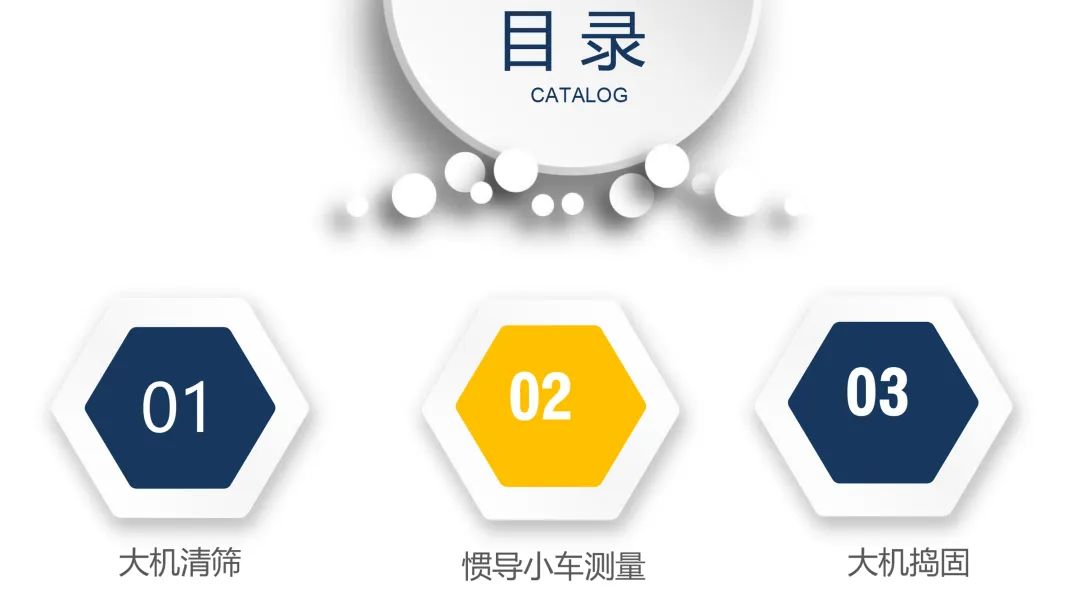
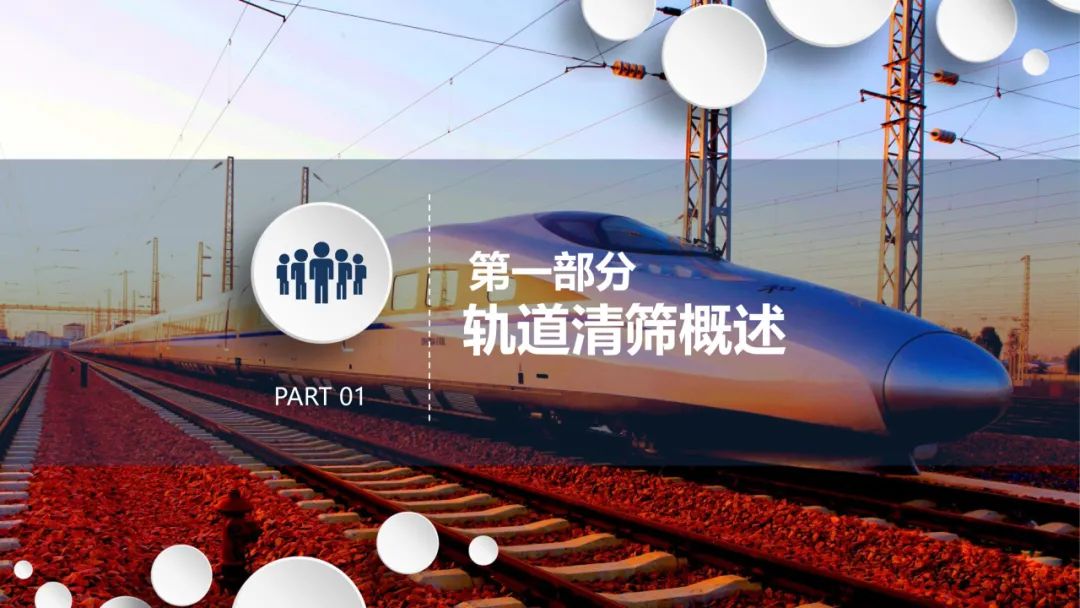
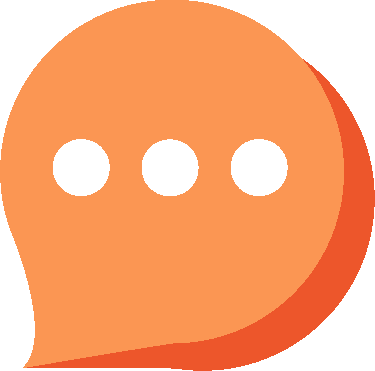
Purpose
The purpose of ballast screening operations is to maintain the cleanliness and drainage of the railway bed, increase the thickness and elasticity of the ballast, and ensure the safety and smooth operation of the railway line. The specific tasks of large machinery ballast screening include removing silt, sand, and contaminated soil from the ballast, sieving and refilling clean ballast, as well as performing track ballast distribution, compaction, and stabilization work.
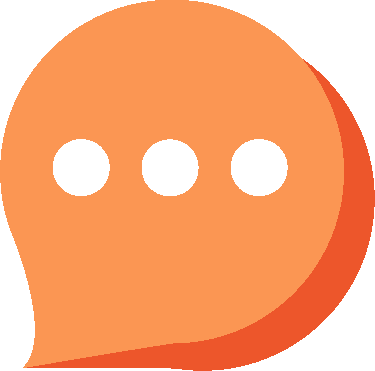
Large machinery ballast screening site
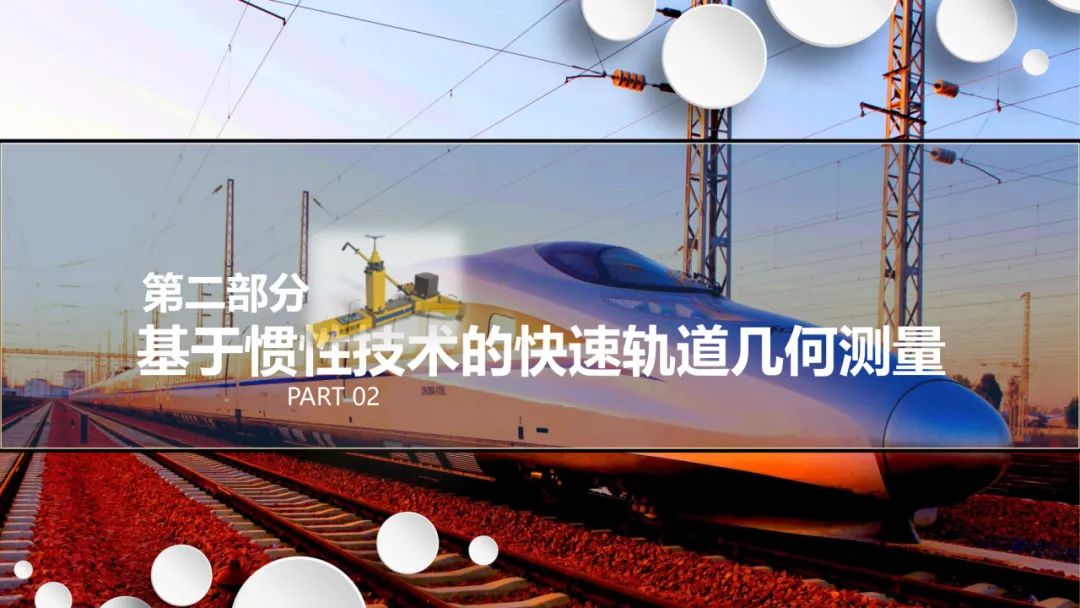
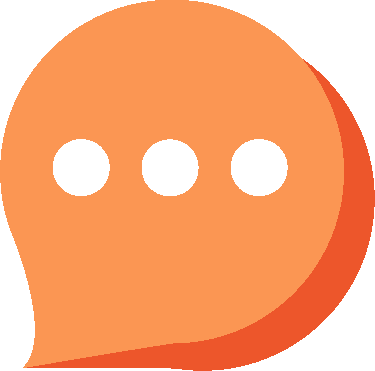
AIS800 GInertial Navigation Rapid Track Geometry State Measurement Instrument
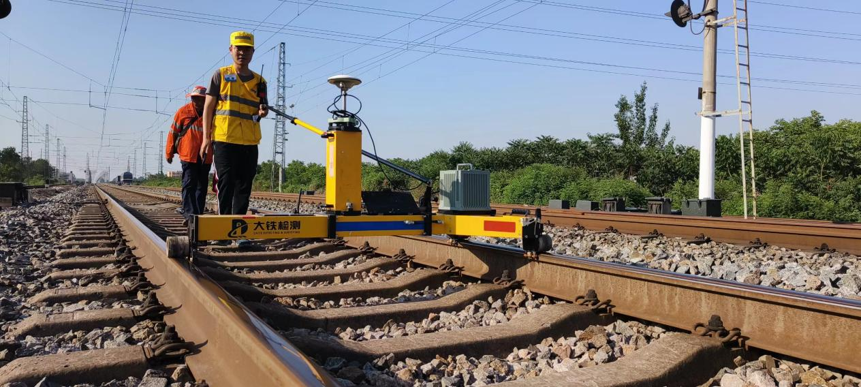
The AIS800G is a track geometry state measurement instrument based on a tactical-grade combined inertial navigation module. After the GNSS data is processed with PPK (Post-Processing Kinematics), the positioning results are fused with the original inertial navigation data (acceleration and angular velocity signals) to obtain the three-dimensional position coordinates of the measurement center. Finally, the three-dimensional position coordinates of the inertial navigation center are projected onto the top surfaces of the left and right rails.The technical highlights include: Based on satellite control and GNSS reference stations, it completes the "absolute + relative" measurement of conventional speed railway tracks, achieving precise unification of the mileage system, accurate positioning of the four major points of horizontal curves, determination of the start and end points of vertical curves, reducing track TQI while maintaining the track's linear shape and position.
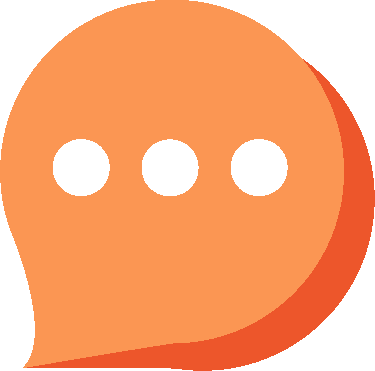
Field Operation Procedure
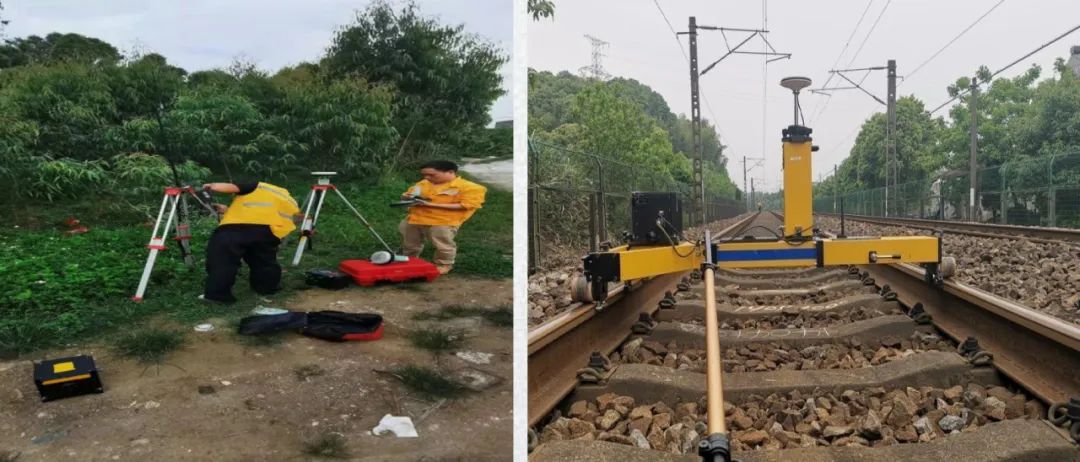
GNSS Measurement:
1. Install GNSS Base Station
2. Quickly Assemble the Measuring Instrument
3. Measurement APP Confirms Operation Information
4. Ensure the measuring wheel is in close contact with the rail
5. Begin Measurement
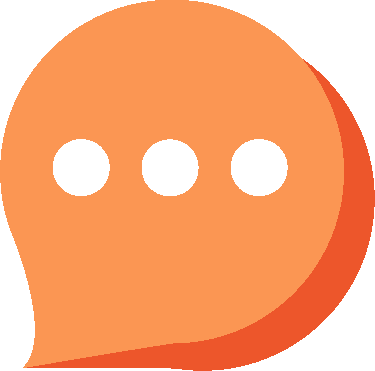
Data Processing
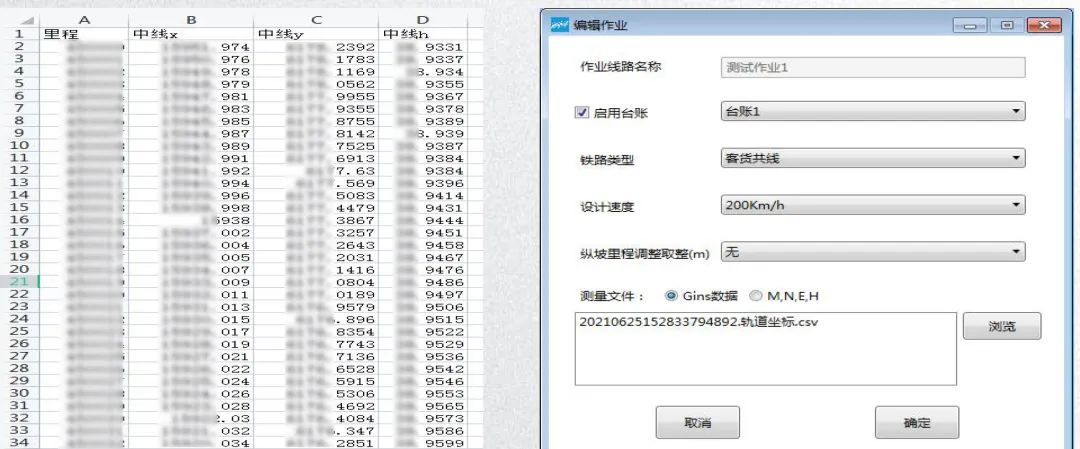
After acquiring the track geometric parameters at a speed of 5-10 kilometers per hour, the actual design line type that best fits is fitted, and line element recognition enables the automatic calculation of track measurement data for line shape segmentation points, determining the line shape at the location of the track measurement points.
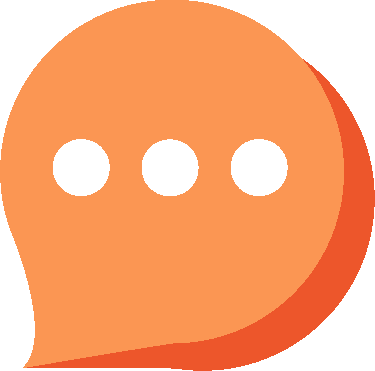
Line Element Recognition
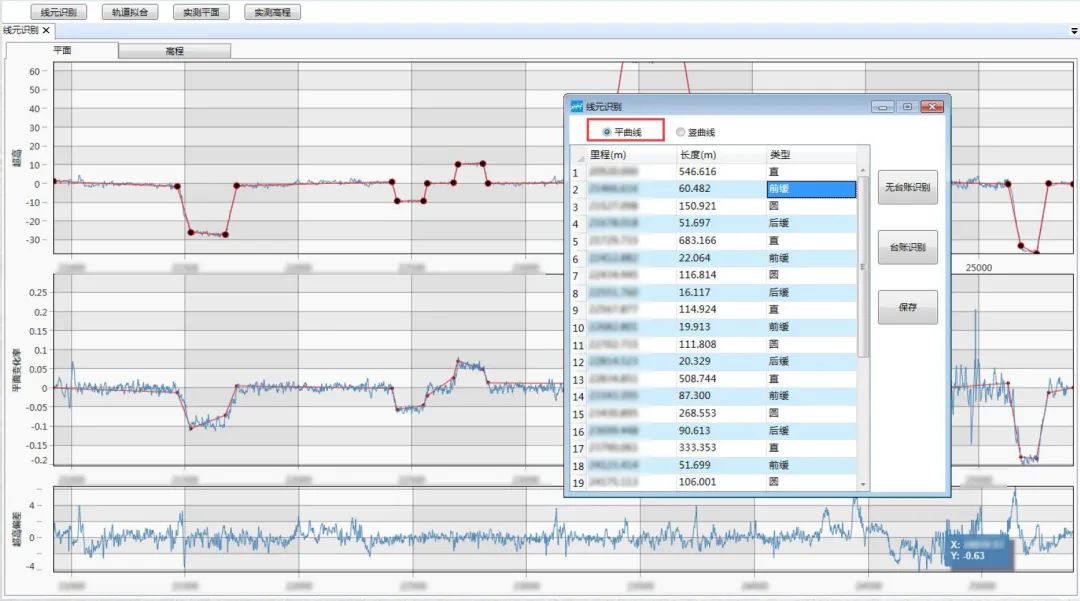
Horizontal Curve Line Element Recognition
A complete plane line form consists of five line elements, which are the approach tangent, the transition curve, the circular curve, the exit transition curve, and the departure tangent. They are segmented by four line element boundary points, which are the point of intersection (ZH), the point of curve (HY), the point of tangency (YH), and the point of intersection (HZ). (For more information, consult DaTie technical staff)
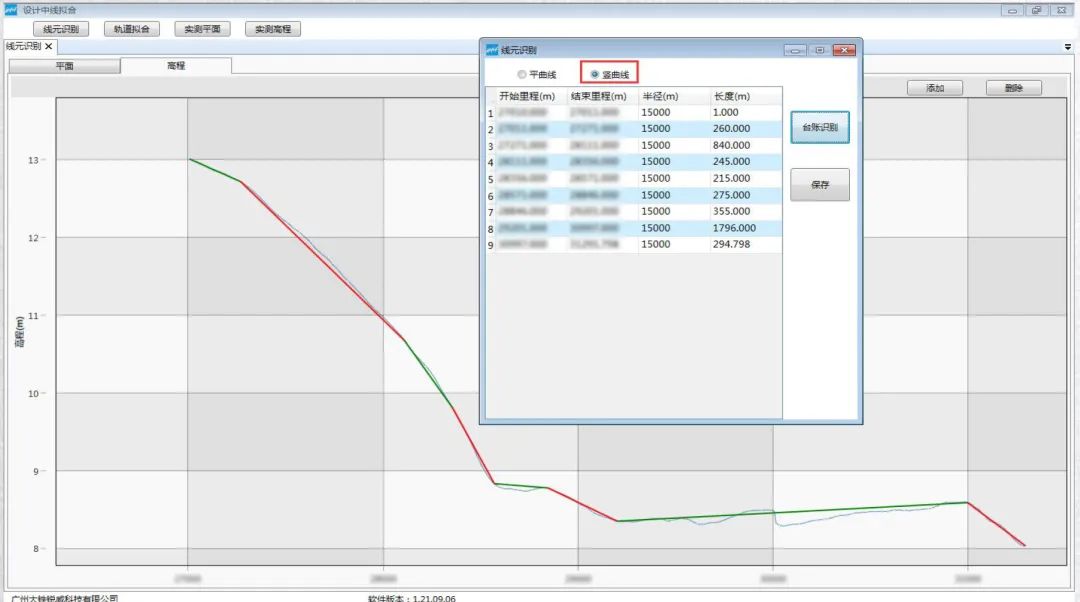
Vertical Curve Line Element Recognition
The vertical profile of a railway line is composed of slope sections with varying lengths and gradients. The intersection point of two adjacent vertical gradients on the railway vertical profile is called the gradient change point. To ensure the safety and comfort of train travel, vertical curves are required at the points where the gradients change. (For more information, consult DaTie technical staff)
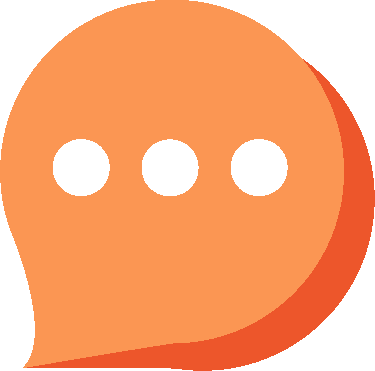
Track Fitting
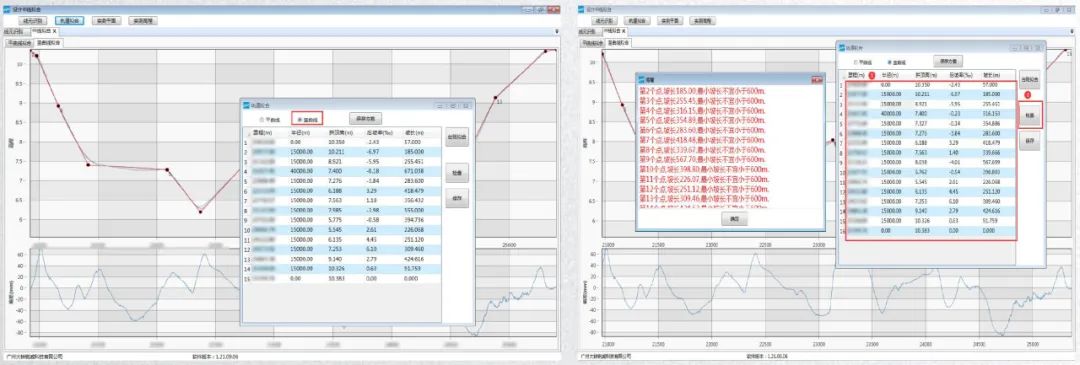
Vertical Curve Adjustment Fitting
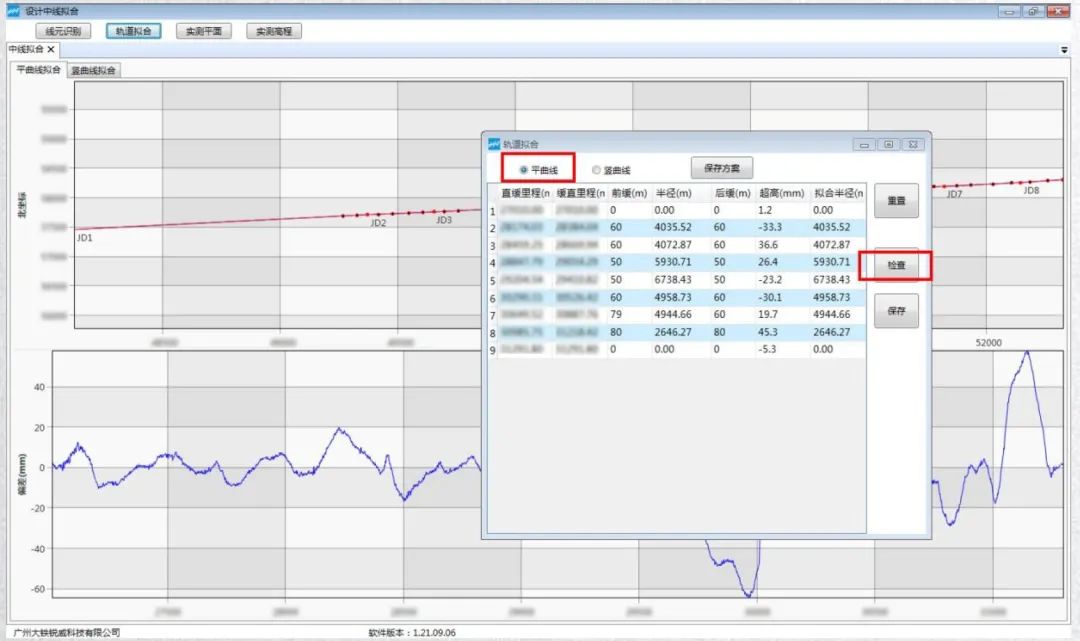
Horizontal Curve Adjustment
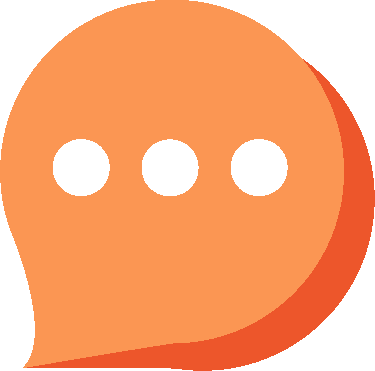
Results Output
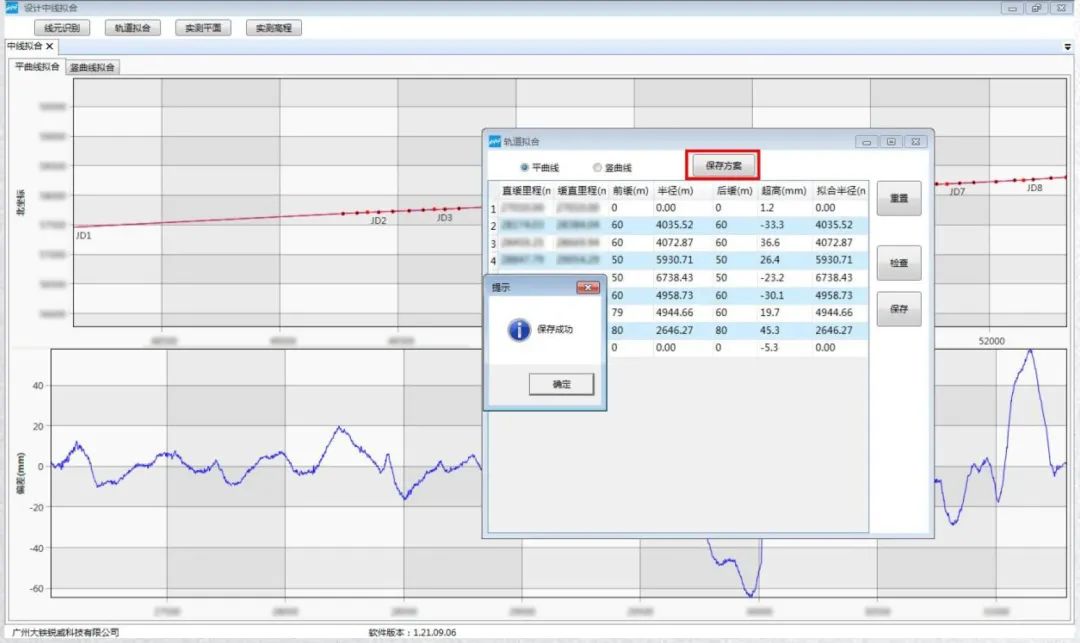
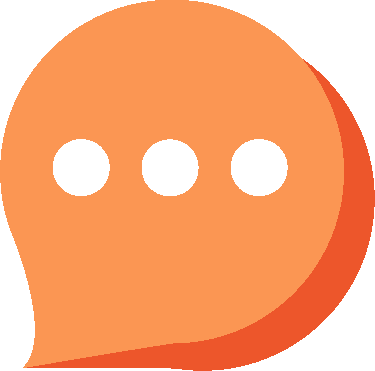
Results Presentation
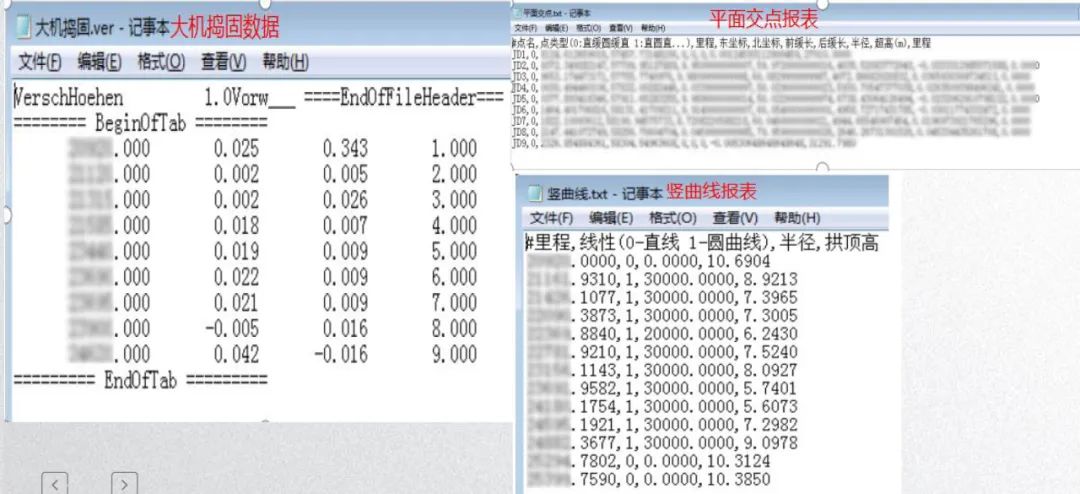
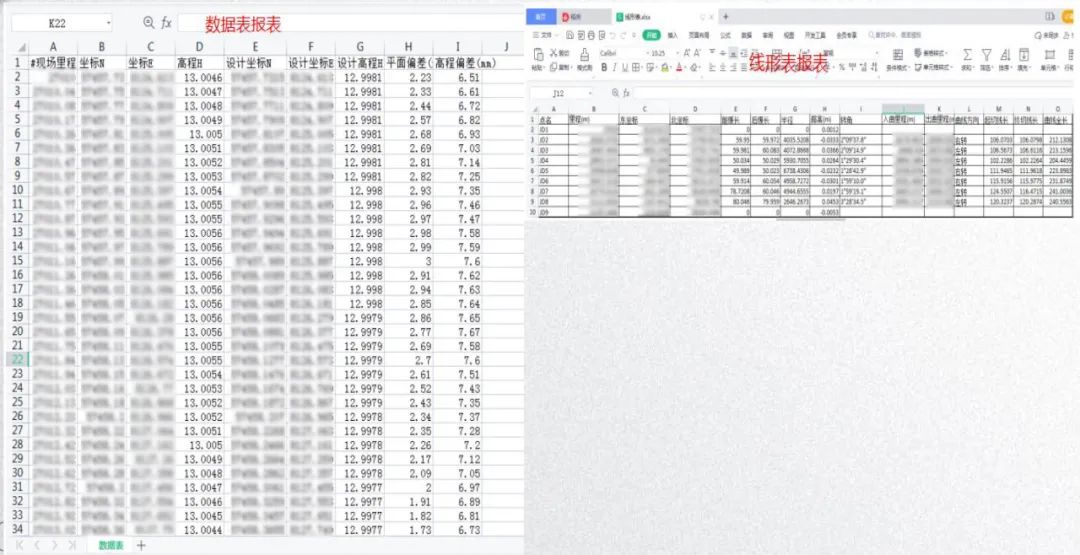
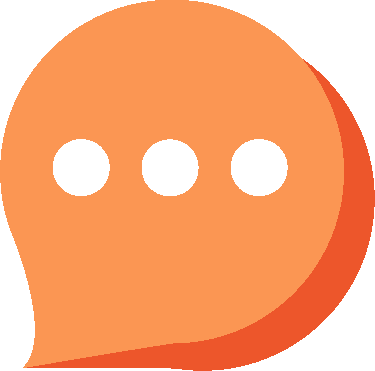
Large Machine Tamping
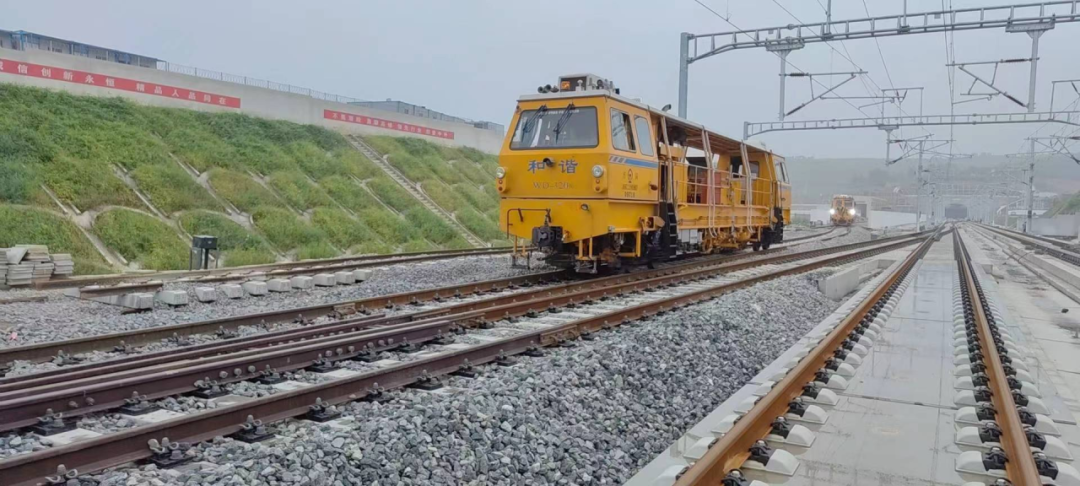
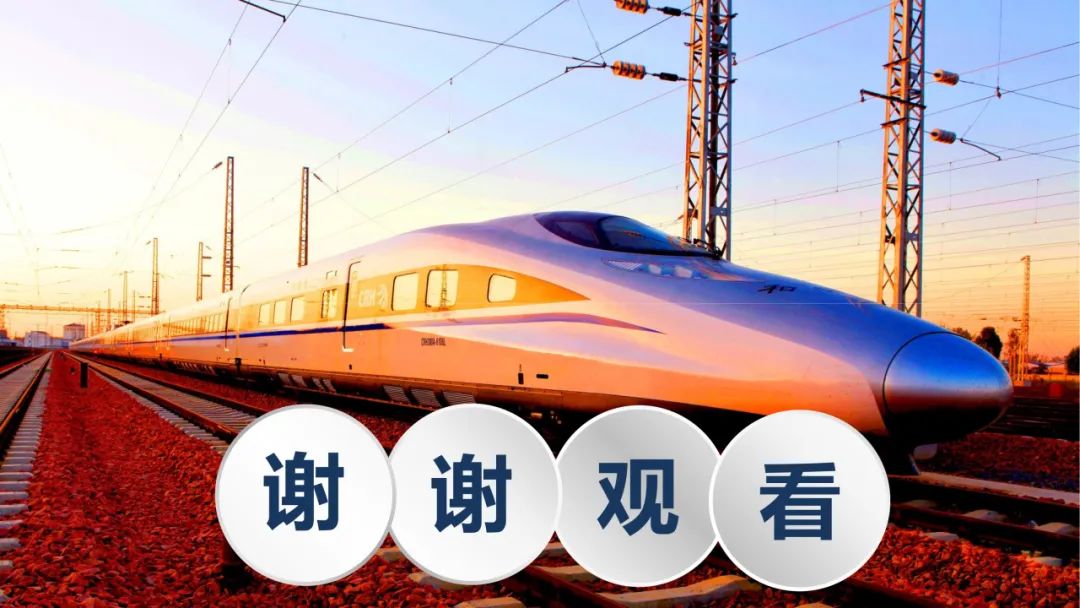
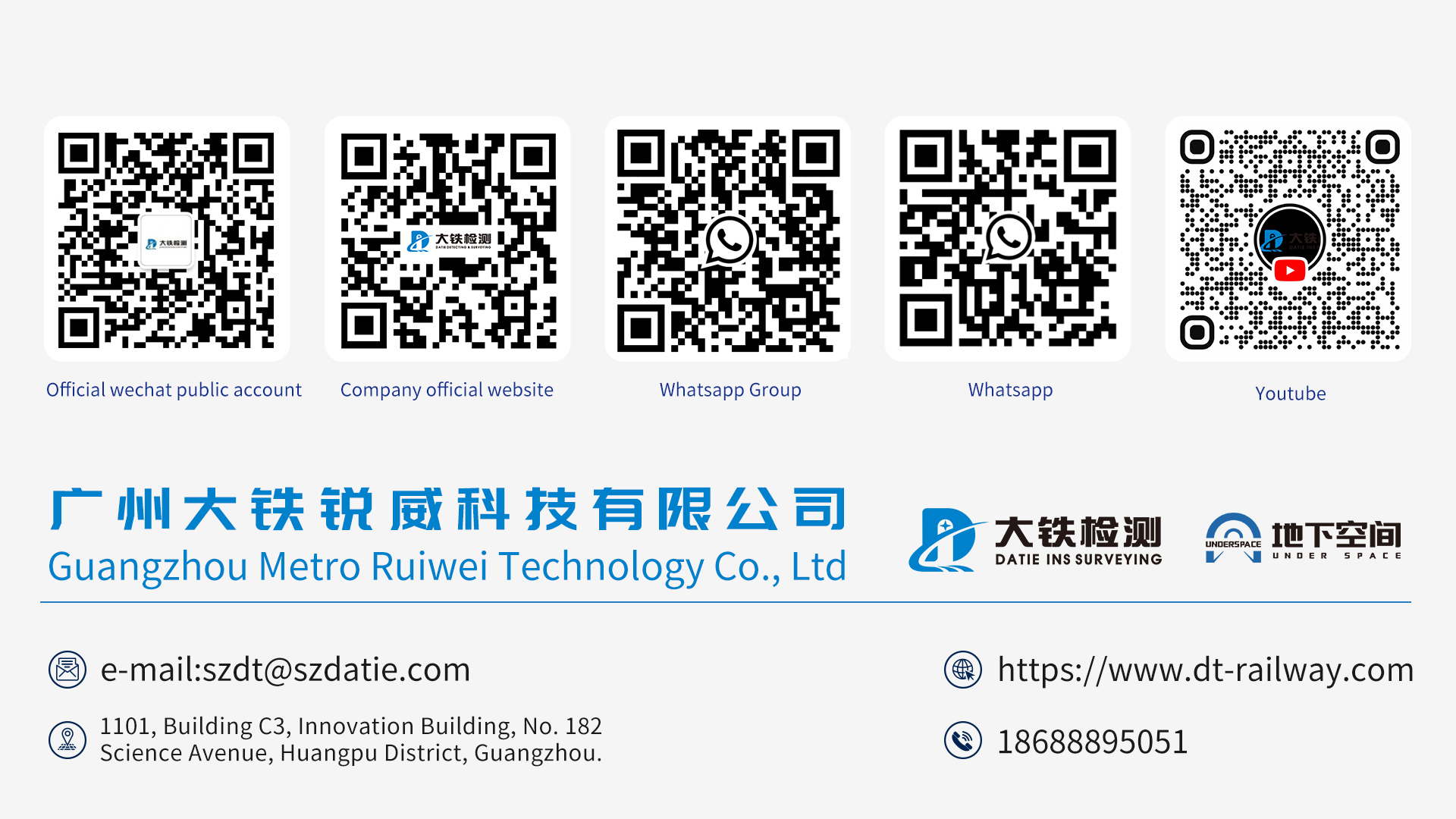